Lithium-ion Battery Manufacturing consultancy
PR Newswire: The battery market is growing at an unprecedented rate, and the electrification of the transportation industry, energy storage for the grid, and many other devices continue to spur this industry’s growth. However, scaling up lithium-ion battery production to meet the increasing demand faces several challenges, including the availability of raw materials, supply chain disruptions, shortages of labor and materials.
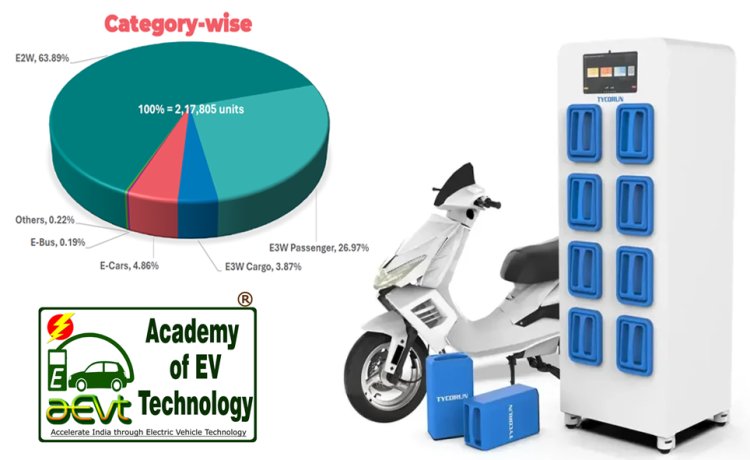
Lithium-ion battery (LIB) manufacturing consultancy is required due to the complexity and rapidly evolving nature of the industry, demanding expertise across various aspects. Consultancies provide specialized knowledge to navigate challenges, optimize processes, and ensure successful implementation of LIB manufacturing projects. Lithium-ion battery manufacturing for electric two-wheelers involves creating battery packs that are compact, lightweight, and provide sufficient power for the vehicle's range. Manufacturers often offer customized solutions for different electric vehicle types, like E-Scooters, E-Bikes, and E-Rickshaws.
Related Post: Challenges and opportunities for high-quality Lithium-ion Battery Manufacturing
Addressing these challenges is crucial to ensure the production of high-quality and efficient lithium-ion batteries. A lithium-ion battery manufacturing consultant assists businesses in the design, development, and production of these batteries, offering expertise in various aspects from initial planning to quality control and troubleshooting.
Here's a more detailed breakdown of why consultancy is crucial:
-
Technical Expertise:LIB manufacturing involves intricate processes like electrode preparation, cell assembly, and electrolyte development, requiring specialized technical knowledge. Manufacturing of industrial lithium-ion batteries is a complex and big challenging process. To achieve consistent quality and safety standards battery pack, requires precise engineering and advanced manufacturing technologies. Any mistake in the assembly process can cause performance problems or safety risks. Strict quality control procedures are essential to ensure battery performance and safety.Consultants can help optimize manufacturing workflows, improve efficiency, and reduce costs by identifying bottlenecks and implementing best practices. Consultants can help implement robust quality control systems and procedures.
-
Supply Chain Management:Ensuring a consistent supply of pack/module manufacturing machinaries, Cells, BMS, BTMS and other components especially with fluctuating prices and geopolitical risks, requires careful supply chain management. Reliance on specific regions for raw materials exposes manufacturers to geopolitical and trade-related risks. Securing a stable and ethical supply of raw materials is a significant challenge. At each stage of the production process, there are supply chain issues that should be addressed during contractual negotiations rather than waiting for the issues to arise during production.Consultants can help develop strategies for securing materials supply chain and managing supply chain disruptions.
-
Technological Advancements:The LIB industry is constantly evolving, with new chemistries and manufacturing technologies emerging. These advancements aim to increase energy density, charging speed, and safety while addressing limitations in traditional lithium-ion batteries. Lithium-ion battery pack manufacturing consultancies are driving technological advancements by focusing on innovations like insights into the latest technologies and help companies stay competitive.India needs to invest more in research and development to close the technology gap with global leaders in battery manufacturing.
-
Battery Management Systems (BMS) and Software:AI-driven BMS are being developed to optimize battery performance, extend life, and ensure safety. These systems leverage data analytics to monitor battery health, predict failures, and manage charging/discharging processes.A consultancy specializing in Battery Management Systems (BMS) for lithium-ion battery packs provides expert guidance and services throughout the battery pack manufacturing process. This includes design, development, testing, and implementation of BMS solutions, ensuring optimal battery performance, safety, and longevity. Consultancies often offer a range of services, from initial feasibility studies to ongoing support and maintenance, helping manufacturers navigate the complexities of Li-ion battery technology.
-
BMS Design and Development:Developing custom BMS solutions tailored to specific battery pack requirements, considering factors like voltage, current, capacity, and application.
-
BMS Testing and Validation:Ensuring the BMS functions as intended and meets safety standards, including over-voltage, over-current, and temperature protection.
-
-
-
Safety and Environmental Concerns:Lithium-ion batteries are known for their energy density, but safety and reliability are crucial considerations during manufacturing. LIB manufacturing involves hazardous materials and processes that require adherence to safety regulations and environmental standards. Ensuring battery safety, including preventing thermal runaway and addressing other potential hazards, is a crucial consideration.Consultants can help implement safe practices and minimize environmental impact.
-
Feasibility Studies:A feasibility study for lithium-ion battery pack manufacturing in India assesses the viability of setting up such a plant by analyzing market demand, raw material availability, production costs, and technological feasibility.
-
Market Analysis:This section assesses the current and projected demand for lithium-ion batteries, considering factors like the growth of electric vehicles, energy storage systems, and other applications.
-
Production Cost Analysis:This involves assessing all costs associated with manufacturing, including labor, energy, equipment, and other operational expenses.
-
Technological Feasibility:The study evaluates the available technology and infrastructure required for battery pack manufacturing, ensuring that the project is technically sound.
-
Financial Analysis:This involves developing a comprehensive financial model that includes project costs, revenue projections, and return on investment calculations.
-
Competitor Analysis:The study analyzes the existing competitive landscape, identifying potential competitors and their market share.
-
Environmental Impact:The study considers the environmental impact of battery manufacturing and recycling, including potential waste disposal and pollution concerns.
-
Regulatory Compliance:Consultants help ensure that manufacturers comply with relevant regulations and standards related to battery manufacturing and safety.
-
Factory Audits:Consultants conduct factory audits to assess manufacturing processes, quality control measures, and safety procedures.
-
Training and Mentorship:Consultants often provide training to manufacturing staff, ensuring they understand the intricacies of lithium-ion battery technology and manufacturing processes.
-
Research and Development:Consultants can contribute to the development of new battery chemistries, materials, and manufacturing techniques, staying ahead of the curve in a rapidly evolving industry.
Consultants can conduct feasibility studies to assess the viability of a LIB manufacturing project, considering technical, economic, and regulatory factors. -
-
Design and Engineering:Lithium-ion battery pack manufacturing design and engineering consultancy provides expert services to companies looking to develop, optimize, or manufacture lithium-ion battery packs.Consultants will help with the overall architecture of the battery pack, including cell selection, pack layout, and thermal management systems and analyze the causes of battery pack failures and provide recommendations for preventing future issues. They can assist with the design and engineering of manufacturing facilities and equipment, ensuring efficient and reliable operation. Consultants can assist in building and testing prototypes to validate designs and ensure they meet performance requirements for electric vehicles, energy storage systems, or other applications.
4. Strategic Guidance and Support:
-
Design and Planning:This phase involves extensive simulations and modeling to predict performance and identify potential issues.
-
Material Selection:Based on the design specifications, suitable materials are chosen.Advanced materials science plays a crucial role in developing materials that meet the specific needs of each module.
-
Manufacturing:Once materials are selected, the manufacturing phase begins.Each technique is chosen based on the nature of the component and the desired precision and efficiency.
-
Assembly:This assembly process can involve various methods, including mechanical fastening (screws, bolts), adhesives, welding, and soldering. The choice of assembly method depends on the materials and the intended use of the module.
-
Testing and Quality Control:This phase involves functional testing, stress testing, and quality inspections to detect any defects or inconsistencies. Advanced testing technologies, such as automated inspection systems and non-destructive testing methods, are often employed to enhance accuracy and reliability.
5. Step-by-Step Assembly Process:
-
Component Preparation:This preparation stage involves cleaning, sorting, and pre-assembling sub-components to streamline the final assembly process.
-
Sub-Assembly:These sub-assemblies consist of several components combined into a functional unit, which will later be integrated into the final product.
-
Final Assembly:The sub-assemblies and individual components are brought together to form the final product. This stage involves precise alignment and fitting of parts, often using automated assembly lines and robotic systems to ensure high accuracy and consistency.
-
Testing:Once the final assembly is complete, the product undergoes various tests to verify its functionality, performance, and safety.
-
Packaging:After passing all tests, the final product is packaged for distribution. Packaging ensures that the product is protected during transit and storage, maintaining its integrity and functionality until it reaches the end user.
-
Quality control:Quality control is a critical aspect of both production and assembly processes. It involves systematic methods to ensure that products meet specified quality standards and are free from defects.
-
A consulting firm specializing in renewable energy, energy storage, and EV technologies, including lithium-ion batteries.
Conclusion
The production and supply chain of industrial lithium-ion batteries face various challenges, including problems with sourcing materials, difficulties in manufacturing, and issues with logistics. To tackle these problems, we can look into using different materials, improving manufacturing processes, building stronger local supply chains, and improving recycling methods.
As technology continues to advance, these processes are becoming more sophisticated, offering new opportunities for innovation and improvement. By embracing technological advancements and adhering to best practices in quality control, manufacturers can enhance their productivity, reduce costs, and deliver superior products to the market.
To meet the growing demand for industrial lithium ion batteries sustainably, ongoing innovation and collaboration across industries, governments, and research institutions are essential. The future of manufacturing lies in the continuous evolution of these processes, driven by innovation and a commitment to excellence.
ESS News: Energy storage system development, latest news, press release, analysis and opinion from the global energy storage industry.